Managing Director of the Liberty Tubular Solutions, Phil Begley and Adrian Bailey, MP for West Bromwich West at Liberty Industries Group headquarters in Oldbury
A Black Country engineering business is playing a lead role in a new ‘industrial revolution’ designed to forge a low-carbon, sustainable future for Britain’s manufacturing.
During a special briefing at the Liberty Industries Group headquarters in Oldbury, Adrian Bailey, MP for West Bromwich West, heard from company directors how the products the company makes in the Midlands for the automotive and other industries will be based increasingly on sustainable production methods.
Adrian, who has chaired key Parliamentary select committees for business and currently chairs the All-Party Group on aluminium, made a fact-finding visit to the plant to learn more about the firm’s GREENSTEEL and GREENALUMINIUMstrategies which are leading the way to a UK industrial revival based on renewable energy and recycling.
Liberty currently employs more than 2,500 people in the West Midlands and, following more than two years of acquisitions and growth, is now one of Britain’s largest private industrial employers with around 5,500 staff.
Phil Begley, managing director of the Liberty Tubular Solutions division told Adrian that some of the products from the flagship Oldbury site are already being made from steel produced in Liberty’s own mills using renewable energy from sister company SIMEC.
He added that an increasing proportion of the firm’s steel and aluminium products would come from such sources in the future. Aluminium is already made at Liberty’s Fort William smelter which is powered by hydro and bio-liquid and there are plans add wind power to the plant’s energy mix.
Moreover, Phil said that more and more of Liberty’s engineered products would be based on recycled steel, melted from the country’s fast-growing supply of scrap metal. Liberty’s strategy is to invest in UK furnaces that can melt up to five million tonnes a year of scrap, turning it into high quality steel.
He said: “Using sustainable methods to produce steel and engineered products not only makes environmental sense but also makes economic sense because it will enable Britain’s steel and engineering sectors to become more competitive and therefore more sustainable.”
Following the visit and tour of the Oldbury plant Adrian said: “The Black Country had a flagship role in the original Industrial Revolution so it is particularly appropriate that it should be a standard bearer for a new green industrial revolution that will hopefully protect and create skilled jobs and give the region and the country a strong and prosperous industrial future.”
Latest News
View All
LIBERTY proposes new measures to drive demand for UK steel production and stimulate investment
LIBERTY Steel’s submission to the UK Steel Strategy consultation has proposed decisive Government action in the form of strategic demand...
View
Whyalla steelworks up and rolling again
Another milestone following blast furnace restart The resumption of steel production in the Whyalla Steelworks has reached another milestone with...
View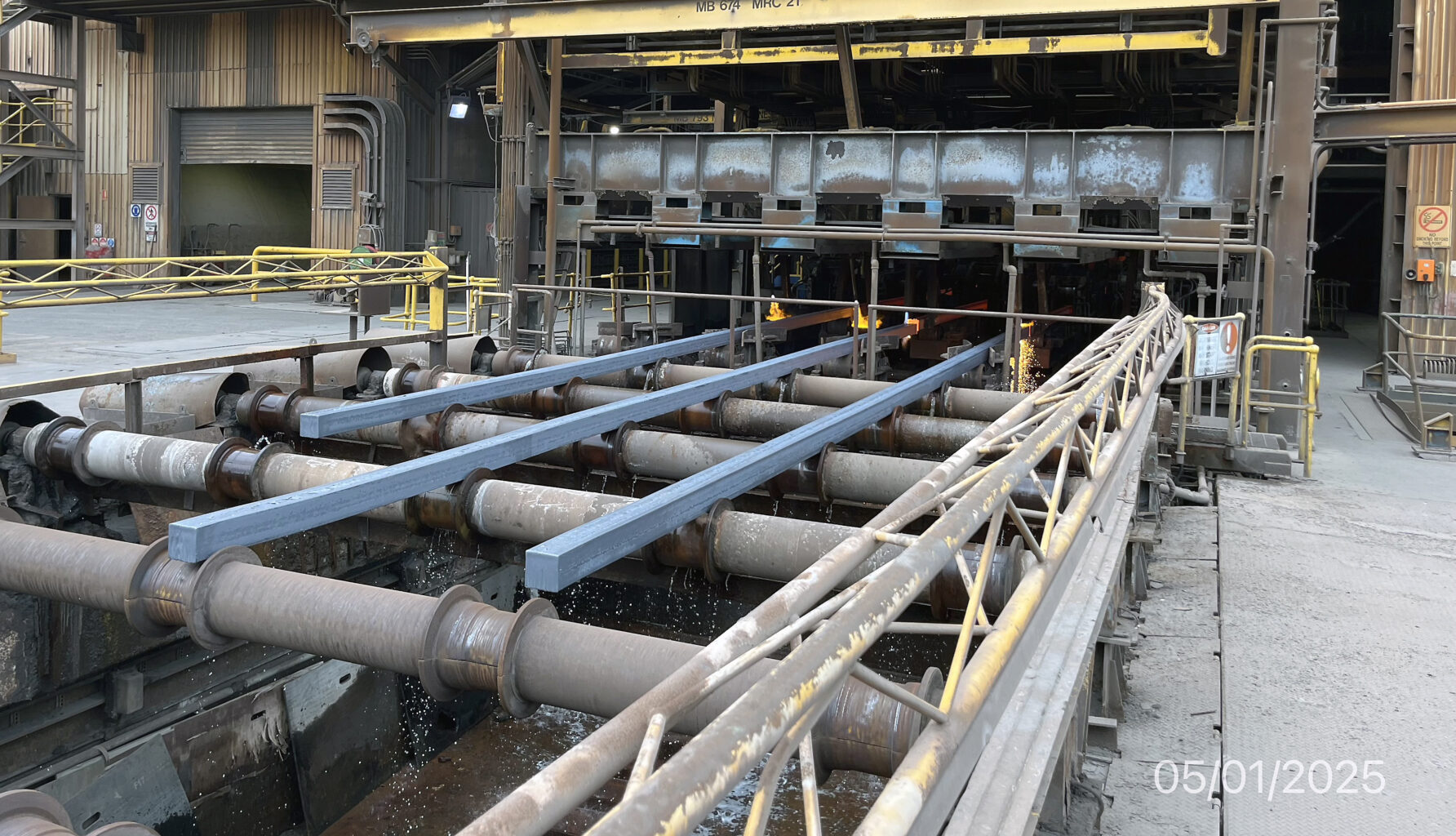
Whyalla steel production restarts but GFG cautious
Whyalla Steelworks has cast its first steel following a 4-month shut down due to operational challenges and extensive repairs. The...
View
Introducing the Steel Town Podcast: A glimpse into the heart of steelmaking in Whyalla
GFG Alliance has launched Steel Town, a new podcast series that takes listeners into the world of mining and steelmaking in...
View