LIBERTY Galati GREENSTEEL transformation
We will innovate to drive the transition to a low-carbon economy which ensures a sustainable future for us and future generations.
LIBERTY Steel Group aims to invest up to €1 billion over the next seven years in the LIBERTY Galati GREENSTEEL transformation plan. This plan is part of LIBERTY’s strategic ambition to be carbon neutral production by 2030 (its CN30).
The strategy will ensure the long-term economic, social, and environmental sustainability of LIBERTY Galati so that it can reinvest profits and continue to provide high quality steel and jobs for future generations.
LIBERTY Galati’s transformation plan to become a carbon-neutral GREENSTEEL supplier by 2030 – mixing new and innovative steelmaking technologies with renewable energy – will help Romania be a leader in the environmentally friendly production of a material essential in building our country’s future.
The GREENSTEEL Transformation Plan requires:
Energy efficiency and carbon reduction projects in existing operations. | |
Two hybrid electric arc furnaces (EAFs) which are expected to reduce CO2 emissions per tonne of steel produced by up to 80%. | |
A Direct Reduced Iron (DRI) plant that will initially use natural gas before transitioning to green hydrogen. | |
An integrated MI.DA mini-mill which can increase production to 4 million tonnes per year from 3 million tonnes per year, with that additional volume focused on long products. | |
To maximize the consumption of renewable energy and to reduce overall electricity consumption, LIBERTY Galați will install a 180MW photovoltaic (solar) park and a 20MW wind farm, developed by SIMEC. | |
The plan is supported by the GREENSTEEL Academy, which aims to upskill current employees and attract younger people into the industry, and the GFG Foundation, which already runs several programmes with universities and high schools in Romania aimed at educating the younger generation and developing local communities. |
The Direct Reduced Iron (DRI)
The Direct Reduced Iron (DRI) process, especially when using green hydrogen, is the most effective technology steel producers can use to reduce their carbon emissions and rapidly transition to decarbonised green steel. The objective of a DRI plant is to remove the oxygen from iron ore, to create metallised iron, without melting it. This is achieved using a reductant to remove the oxygen in the ore and results in water instead of CO2 emissions. This process produces a carbon neutral DRI which can then be used to make steel. The DRI can also be made into a Hot Briquetted Iron (HBI) product making it suitable for transporting.
Hybrid EAFs
Hybrid electric arc furnaces, such as those we will installing in Galati, have emerged as an innovative solution for integrated steel manufacturers to transition away from conventional blast furnace (BF) production to electric steel production – GREENSTEEL technology. This technology allows hybrid furnaces to be more flexible in the charge mix, from large quantities of DRI/HBI (direct reduction iron/iron) to up to 100% steel scrap.
This hybrid technology is also more energy efficient, has lower operating costs, reduces plants’ reliance on imported coal, and provide them with even greater production flexibility in the future, so that they can respond even more effectively to changing market conditions.
Hydrogen steelmaking
The technology for Hydrogen production is proven but still needs to delivered at an industrial level. Hydrogen, as part of water, is the most abundant universal element in nature, but generally doesn’t appear in its elemental molecule. It requires energy to separate the hydrogen and oxygen molecules, through the process of electrolysis, which can be done a number of ways. Using the more traditional alkaline electrolysis process, a strong electrical current from normal or renewable energy sources, is passed through a tank of alkaline water solution to split the water molecules into two constituent elements: Hydrogen and Oxygen. Each element can then be stored separately while the waste H2O, or water, which is created as part of the process can be endlessly recycled to create more Hydrogen.
The importance of our people to our GREENSTEEL journey
GREENSTEEL is not just a new type of steel, it is something revolutionary, and every person at LIBERTY must be aware of the importance of their involvement and that they are an integral part in this major technological change.
STRONG, GOOD, DEDICATED people, all people of steel, will make this possible.
We recognize their contribution, the more than 5000 people working at the steelworks and look forward to them being partners in building the future together.
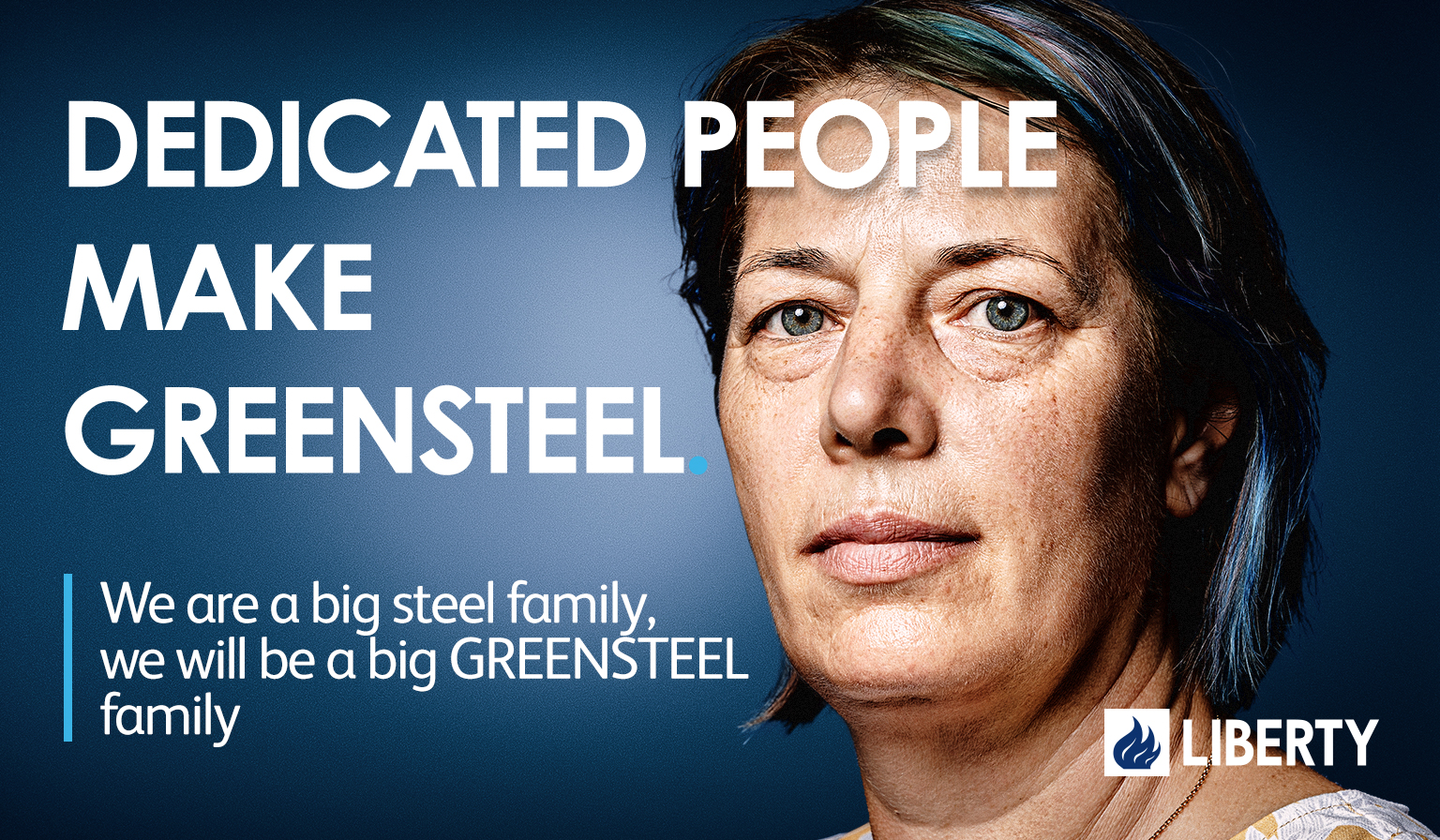